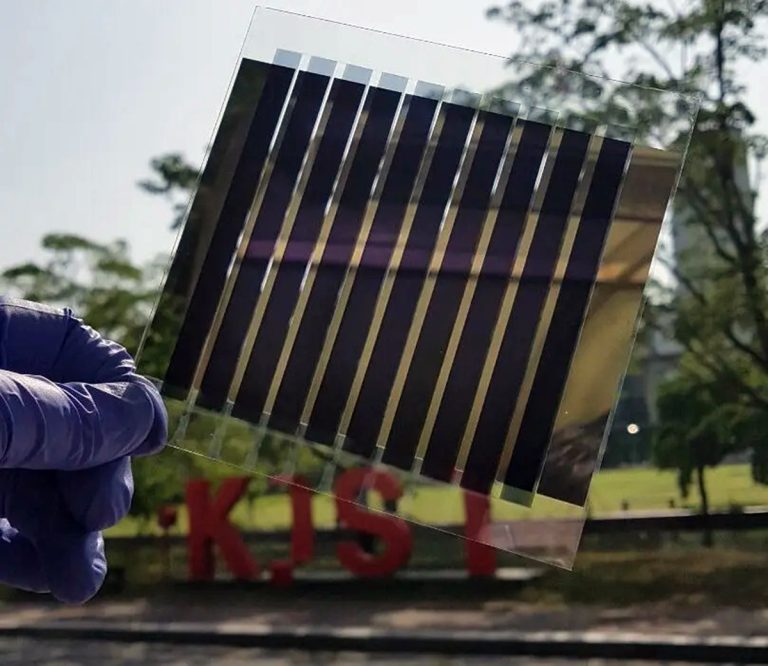
Un team coreano ha sviluppato nuovi additivi polimerici per prevenire il degrado dei moduli stampati di fotovoltaico organico
Poter stampare le celle solari rappresenta uno dei grandi vantaggi del fotovoltaico organico, assieme ai bassi costi e all’eco-compatibilità dei materiali. Per questo segmento solare esistono, tuttavia, ancora grandi ostacoli sia a livello produttivo che di prestazioni. A cominciare dalla difficoltà di estendere l’area fotoattiva, la parte della cella che assorbe la luce solare convertendola in elettricità. A livello di laboratorio, infatti, 0,1 cm2 di strato fotoattivo riescono a dare il meglio di questa tecnologia. Ma passare a dimissioni adatte alla commercializzazione e all’applicazione pratica, è impegnativo e può portare ad un degrado delle prestazioni.
Il gruppo di ricerca guidato dal Dottor Hae Jung Son del Korea Institute of Science and Technology (KIST) ha scoperto i fattori alla base di questo deterioramento e creato una contro ricetta per stampare celle solari organiche di grandi dimensione efficienti e stabili. L’ingrediente segreto? Un nuovo materiale additivo polimerico.
Il problema del fotovoltaico organico risiede nel processo produttivo. Su scala di laboratorio per realizzare gli strati fotoattivi è impiegato lo spin coating o rivestimento per rotazione. In poche parole, si deposita una soluzione – contenente in questo caso molecole organiche fotoattive – su un substrato che successivamente viene fatto ruotare ad alta velocità . Il processo permette di ottimizzare la distribuzione delle molecole e far evaporare il solvente. Su ampie aree, tuttavia, la velocità di evaporazione risulta troppo lenta, dando origine ad aggregazioni tra i materiali.
L’additivo polimerico, creato dagli scienziati coreani, previene questo fenomeno interagendo con le stesse molecole organiche. Inoltre, grazie ad un controllo della struttura a livello nanometrico, è possibile migliorare le prestazioni e la stabilità delle celle solari. Il team ha raggiunto un’efficienza del modulo del 14,7%, con un aumento della resa del 23,5% rispetto a ai sistemi convenzionali. L’efficienza è stata mantenuta oltre l’84% del valore iniziale per 1.000 ore, anche in un ambiente riscaldato a 85°C. I risultati sono stati pubblicati su Nano Energy (testo in inglese).